Ventilsitzbearbeitung, ein Jahrhundert Entwicklung und … die Lösung!
Vor
Eintauchen
und das Hartmetall-Formwerkzeug
Zeichnung 1 Rattermarken
|
Zeichnung 2 Wellen
|
Beim Läppen von Ventilsitzen aus Pulvermetall oder einigen Ventilsitzen aus Gusseisen entstehen unvermeidliche Rattermarken. Rattermarken sind für ein Ventil sehr schädlich, da bei geschlossenem Ventil Gase durch sie entweichen.
Der bearbeitete Ventilsitz verformt sich folglich schnell und seine Abdichtung wird nie ausreichend sein. Rattermarken entstehen, wenn Hartmetallformwerkzeuge eine große Oberfläche eines Materials mit körniger Struktur aus unterschiedlichen Materialien (wie Pulvermetallen, Sphäroguss usw.) abschaben.
Herkömmliche Ventilsitze, die mit der Läpptechnik (Formwerkzeuge) bearbeitet werden, weisen alle Unebenheiten im Hundertstelmillimeterbereich auf, die das direkte Ergebnis unregelmäßiger Schnittkräfte bei einer 360-Grad-Drehung sind. Die Ergebnisse der sich ändernden Schnittkräfte übertragen unregelmäßige Kräfte auf die Maschinenspindeln, die sich je nach Maschine mehr oder weniger biegen und unregelmäßige Formen erzeugen. Dieses Phänomen, das den Bedienern manueller Maschinen wohlbekannt ist, wird bei Auftreten großer sichtbarer Defekte durch schnellen und kräftigen Druck auf den Spindelantrieb ausgeglichen.
Dies führt zu einem erheblichen Spindelaufwand und kann zwar dabei helfen, kleine Defekte zu glätten, die Geometrie jedoch in keiner Weise korrigieren.
Diese Unebenheiten, die dem Prinzip der Bearbeitung durch Läppen innewohnen, haben zweifellos Auswirkungen auf die Ventildichtung und erfordern ein weiteres Läppen jedes Ventils auf seinem Ventilsitz, um eine akzeptable Dichtung zu erhalten. Das Ventilläppen, das bisher von Motorenbauern und ihren Kunden aus der Not heraus akzeptiert wurde, ist seit langem von Motorenherstellern und allen, die die Mindestqualität anstreben, die für die heutigen Motorgenerationen erforderlich ist, verbannt worden.
Jetzt
FIXED-TURNING®
und das Einzelpunktwerkzeug
Zeichnung 3
Geometrische Präzision
Durch die Bearbeitung durch Interpolation, FIXED-TURNING®, werden alle in den Zeichnungen 1 und 2 dargestellten Defekte endgültig beseitigt.
Mikro-Rattermarken und Wellenbildungen sind praktisch unmöglich zu erzeugen. Bei der Einzelpunktbearbeitung ist die Bildung solcher Defekte nicht möglich. Man braucht nur einmal an die Bearbeitung auf einer Drehmaschine zu denken, um sich davon zu überzeugen.
Die Bearbeitung mit einem Drehwerkzeug, das sich auf zwei interpolierten Achsen bewegt, erzeugt eine kreisförmige, perfekt runde Mikronut. Die Tiefe der Nut und der Abstand zwischen zwei Nuten werden durch die numerische Steuerung der Maschine kontrolliert, wodurch die feinsten erreichbaren Oberflächengüten erzielt werden.
Ebenso wie der Schneidaufwand erheblich (300-mal und mehr) reduziert wird, werden auch die Oberflächenfehler auf ein Niveau reduziert, das FIXED-TURNING® an die Spitze der Qualitätsskalen führender OEMs bringt.
eine neue Ära, eine neue Welt voller Möglichkeiten ...
Die Bearbeitung der schwierigsten Zylinderköpfe ist für die längsten Profile, die speziell zur Leistungssteigerung des Motors entwickelt wurden, innerhalb weniger Minuten pro Ventilsitz möglich. Die Bearbeitung eines herkömmlichen „3-Winkel“-Profils erfolgt innerhalb weniger Sekunden.
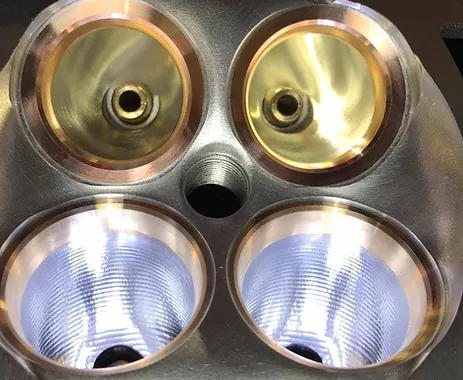
Motorrad-Zylinderköpfe , die kleinsten Ventilsitze, die es gibt und die es geben wird (Downsizing, das Herzstück aller neuen Motorentwicklungsprogramme), können mit größter Leichtigkeit und der optimalen Präzision von Wettbewerbsmotoren bearbeitet werden …
NEWEN®-Maschinen ermöglichen es jedem Motorinstandsetzer, sich als Spezialist für die Bearbeitung aller Motortypen zu positionieren. Die Genauigkeit, die systematisch mit FIXED-TURNING®-Maschinen erreicht wird, gilt für alle Motortypen. Man muss nicht mehr auf die eine oder andere Bearbeitung an diesem oder jenem Zylinderkopftyp verzichten. Alle schwierigen Bearbeitungsvorgänge werden zu einer Quelle zusätzlicher und erheblicher Gewinne.
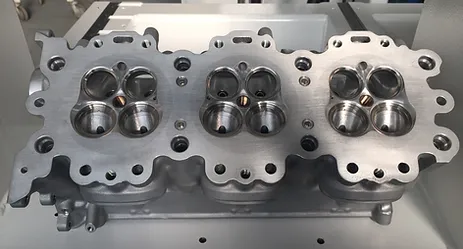
Der Hochleistungsmarkt und der mechanische Freizeitmarkt liegen in der Reichweite jedes Motorinstandsetzers, der mit einer FIXED-TURNING®-Maschine ausgestattet ist.
Die gesamte Präzision, die in der Formel 1 oder anderen anspruchsvollen mechanischen Hochleistungssportarten erforderlich ist, kann automatisch und systematisch erreicht werden. Perfektion ist garantiert.
High-Performance ist ein wachsender und lukrativer Markt. Das Ansehen eines hochqualifizierten Fachmanns, der sich auf dieses Spezialgebiet einlässt, strahlt auf sein gesamtes Unternehmen aus.
Die Kraft-Wärme-Kopplung (KWK), auch bekannt als „Blockheizkraftwerk“, die Umstellung von Motoren auf Erdgas und Biokraftstoffe (Ethanol), erfordert schnelle und präzise Bearbeitungsvorgänge von Ventilsitzsenkungen und sehr harten Ventilsitzen.
Die Prinzipien der Kraft-Wärme-Kopplung sind seit langem bekannt und werden in einer Vielzahl von Anwendungen eingesetzt. Dank der Fortschritte in der Technologie ultrareiner, mit Erdgas betriebener Kolbenmotoren, Wärmetauschern und Systemsteuerungen ist die Kraft-Wärme-Kopplung heute für Anwendungen unterschiedlichster Größenordnung sowohl praktisch als auch wirtschaftlich.
Ein Aspekt der Stromerzeugung, der diese Fortschritte beeinflusst hat, ist der immer stärkere Bedarf an sauberer Energie. Emissionskontrollstrategien, die den Einsatz von mit Erdgas betriebenen Verbrennungsmotoren für KWK- und ICHM-Anwendungen auf einem Niveau ermöglichen, das den aktuellen Standards für Großkraftwerke entspricht oder darunter liegt, haben die Kraft-Wärme-Kopplung noch praktischer, wirtschaftlicher und für eine breitere Palette kommerzieller und industrieller Anwendungen zugänglicher gemacht.
FIXED-TURNING® ist das ideale Werkzeug für diese Dienstleistungen, die einfach, schnell, präzise und sehr profitabel werden.
Mit FIXED-TURNING® ist die Bearbeitung aller Nockenwellenbohrungsgehäuse auf Übermaß, um Übermaßhülsen in die Gehäuse einzusetzen, ein einfacher, präziser und rentabler Vorgang.
Erstellen Sie OFFSET-Profile nach Belieben ...
Bearbeitung von Venturirohren (bis 112 Grad) zur Beschleunigung der Gasgeschwindigkeit.
Venturi: Ein offener Winkel unter dem Sitz, der es ermöglicht, die Geschwindigkeit der Abgase durch Dekompression zu beschleunigen.
Bearbeiten Sie präzise alle Arten von Ventilführungen (Gusseisen, Pulvermetalle, Bronze, alle Legierungen usw.). Reiben Sie Ventilführungen mit höchster Präzision in einem Einzelvorgang oder in einem kombinierten Ventilsitzbearbeitungsvorgang.
Bearbeiten Sie alle hochpräzisen Ventilsitzsenkungen mit einem einzigen Schneidwerkzeug. Zur Vorbereitung von Ventilsitzgehäusen in allen Arten von Zylinderköpfen, aus Gusseisen oder Aluminium, eine präzise und rentable Arbeit für alle FIXED-TURNING®-Profis.
KOMATSU Erdgas-Zylinderkopf Ventilsitzhärte: 56/58HRC (573HB+ / 610HV50+)
- Verwendeter Einsatz: FT-11-11
Schnittgeschwindigkeit: 180 m/min
- Bearbeitungsmodus: Trockenschnitt
- Schneidzyklus: 28 Sek./Sitz
- Rundheit: 1µ bis 2,40µ
Oberflächenbeschaffenheit: 0,20Ra
Eine weitere NEWEN-Exklusivität: die Bearbeitung von Zündkerzengehäusen.
Die Sitze der Dekompressorventile eines Mercedes Actros zu bearbeiten, ist „ein Kinderspiel“.
FIXED-TURNING® und seine numerische Steuerung bieten die Möglichkeit, das Unmögliche auf profitable und wiederholbare Weise zu erreichen.
Eine Technologie für alle.
Alle NEWEN FIXED-TURNING®-Maschinen, einschließlich CONTOUR-BB™, CONTOUR-BB-CS™, CONTOUR™, CONTOUR-CS™, EPOC-VISION™, sind mit einem elektronischen System zur präzisen Wiederholung der Schnitttiefe ausgestattet. Dieses von NEWEN entwickelte System ist kein Messsystem an sich, sondern wurde konzipiert, um eine präzise Wiederholung einer Bearbeitungsposition zu ermöglichen, indem eine zufällige Referenz auf dem zu bearbeitenden Zylinderkopf genommen wird. Im Allgemeinen ist die Referenz für das NEWEN-System die Zylinderkopfdichtungsebene, die auch als Referenz zur Messung der Ventilsitztiefe verwendet wird. Mit einem speziellen Werkzeug können auch andere Oberflächen wie Nockenwellengehäuse verwendet werden.
Ein elektronisches lineares Messgerät, LVDT, (I) ist an die numerische Steuerung der Maschine angeschlossen. Abhängig von der Eindringtiefe der Spitze des LVDT sendet das Messgerät ein elektrisches Signal, mit dem sich die Position des Messgeräts auf weniger als ein Hundertstel Millimeter genau bestimmen lässt.
Diese Position kann gespeichert werden. Sobald die Position gespeichert ist, wird der Spindelvorschubmotor automatisch gestoppt, wenn die Messlehre erneut um den gleichen Betrag zusammengedrückt wird. Dadurch kann die Maschine alle Ventilsitze in Bezug auf einen gewählten Referenzpunkt in der gleichen Tiefe bearbeiten.
Die Messlehre (I) hat eine feste Position in Bezug auf die Achse des Piloten und in Bezug auf die Spindelhülse, an der sie befestigt ist. Diese feste Position bleibt erhalten, wenn sich die Spindel auf ihrem Luftkissen (C) und/oder auf ihrem sphärischen Luftkissen (A) bewegt.
.
Zeichnung 3: Alle Sitze werden gemäß dem gleichen Referenzpunkt (W) bearbeitet, der zur Referenzebene gehört und um ein festes Maß (X) entfernt ist, das mit dem Maß (X) in Zeichnung 1 identisch ist.
Die Abmessung (Z) in Zeichnung 2 ist der Betrag, um den die Lehre komprimiert wird und der einer Bearbeitungsentfernung des Werts (Y) in Zeichnung 2 im Vergleich zum Bezugspunkt entspricht. Dieser Wert (Y) kann mithilfe der gesteuerten Mittel der numerischen Steuerung (Hebevorrichtung, Auswahl der Reparaturabmessungen usw.) von einem vorgegebenen und präzisen Wert abgeändert werden, wodurch die Position der Spitze der Lehre geändert wird. Letzteres wird erneut gespeichert, um beliebig oft wiederholt zu werden.
Der eingefahrene Wert (Z) der Messuhr ist nicht identisch mit dem Spindelhubwert, was hauptsächlich an dem vorhandenen Winkel zwischen der Maschinenspindel und der Messuhr liegt. Außerdem ist der LVDT kein Messinstrument, sondern ein Positionsanzeiger.
Das NEWEN-System zur Automatic Repetitive Depth Control™ garantiert eine identische Tiefenbearbeitung mit Abweichungen von höchstens +/- einem Hundertstel mm.
Es handelt sich um das einzige in der Branche erhältliche System, das eine automatische Bearbeitung mit einer derartigen Präzision garantiert, unabhängig von der Position des Zylinderkopfs im Verhältnis zur Zylinderkopfhalterung, im Verhältnis zum Winkel der Ventilführungen und im Verhältnis zum Hub des Maschinenkopfs.
FIXED-TURNING® UND NUMERISCH GESTEUERTE BEARBEITUNG
Der Zylinderkopf, das neuralgische Zentrum des Motors, vereint alle Funktionen, die die Leistung, die Flexibilität und die Langlebigkeit des Motors bestimmen. Der Zylinderkopf ist das Hauptanliegen von Motorentwicklern und Reparaturspezialisten. NEWEN, FIXED-TURNING® und die numerische Steuerung bieten unvermeidliche und unersetzliche Lösungen für zahlreiche technische Herausforderungen, die mit älteren und/oder traditionellen Technologien nicht gelöst werden können.
BRENNRAUMVOLUMEN
Das Volumen der Kammern, ihr Wert in cm3 (Kubikzentimeter oder CC) und ihre Übereinstimmung untereinander innerhalb desselben Motors sind ein entscheidendes Element für eine optimale und ausgewogene Leistung jedes Zylinders. Nur Kammern mit perfekt ähnlichem Volumen und Form ermöglichen die Leistungsniveaus und Harmonien, die für die hohen Drehzahlen von Hochleistungsmotoren erforderlich sind (siehe „HCCI“-Technologie am Ende dieses Dokuments). 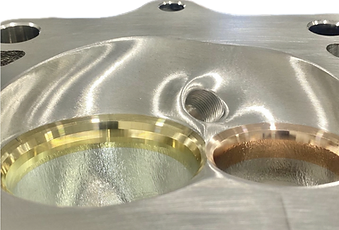
Das FIXED-TURNING® und die numerische Steuerung NEWEN ermöglichen hochpräzise Bearbeitungsvorgänge. Ventilsitze und ihre spezifischen Profile (Einlass und Auslass) können innerhalb von 1/100 mm (0,01 mm oder 0,00039 Zoll), die Bearbeitungstiefen werden automatisch mit einem elektronischen Tiefenmesser und einer hochpräzisen Kinematik gesteuert.
Die exakten Volumina der Kammern werden durch entsprechende Formen und absolut identische Tiefen gewährleistet.
LUFTDICHTIGKEIT DES ZYLINDERS
Für die optimale Funktion des Motors und das Erreichen hoher Drehzahlen ist die sofortige Luftdichtheit des Zylinders von entscheidender Bedeutung.
Der Metall-Metall-Kontakt zwischen Ventil und Ventilsitz muss vollständig und perfekt sein, um diese schwierige Luftdichtigkeitsfunktion zu gewährleisten. Abgesehen von der Qualität der Materialien, die hohe Geschwindigkeiten aushalten, ist der Metall-Metall-Kontakt zwischen Ventil und Ventilsitz die Grundvoraussetzung für eine perfekte und dauerhafte Luftdichtigkeit des Zylinders.
Die perfekte Formübereinstimmung zwischen Ventil und Ventilsitz wird durch die vollständige Einhaltung der Geometrien (Formen, Winkel, Oberflächenbeschaffenheit usw.) der beiden Kontaktflächen ermöglicht.
Nur die hochpräzise Bearbeitung der Ventile und Ventilsitze ermöglicht es, diese wesentliche Übereinstimmung zu erreichen. Das Läppen der Ventile, das in der Vergangenheit aufgrund der mangelnden Präzision bei der Bearbeitung der Ventilsitze und Ventile obligatorisch wurde, ist streng verboten, um die Luftdichtheitsniveaus und die Dauerhaftigkeit der Luftdichtheit zu erreichen.
NEWEN, das FIXED-TURNING® und seine numerische Steuerung ermöglichen die Bearbeitung von Ventilsitzen mit Formfehlern (Rundheit) in der Größenordnung von 3 µm (oder 0,003 mm oder 0,000118 Zoll) oder weniger, je nach den bearbeiteten Materialien. OEMs fordern Rundheitsfehler von nicht mehr als 5 bis 6 µm sowohl für Ventilsitze als auch für Ventile.
NEWEN FIXED-TURNING® und seine numerische Steuerung ermöglichen die Einstellung von Winkeln im Hundertstelgradbereich . So können die Winkel der Ventilsitze und Ventile problemlos eingestellt werden, um eine perfekte und dauerhafte Dichtheit zu erreichen, ohne der zerstörerischen Versuchung des Läppens nachzugeben und dadurch die Form dieser Teile zu verformen.
Die NEWEN FIXED-TURNING®-Maschinen fräsen perfekt runde Ventilsitze mit sehr präzisen Winkeln und die Luftdichtheit ist auch bei vielen Betriebsstunden perfekt.
Die Bearbeitung mit einem Formwerkzeug kann keine präzisen Winkel und perfekt runde Ventilsitze garantieren, daher ist es notwendig, die Ventile zu läppen. Eine Wahl, die zu einer kurzlebigen Luftdichtigkeit führt und die Leistung erheblich reduziert.
AUSRICHTUNG UND KOAXIALITÄTEN Dank der Reduzierung der bewegten Massen mit Hochleistungs-Ventilrückholmechanismen sind erhöhte Motordrehzahlen, schnelle Beschleunigungen und Verzögerungen möglich. All diese Leistungen sind jedoch nur durch eine drastische Reduzierung der Reibung und Versteifung der bewegten Teile, Ventile, Nockenwellen, Einlassnocken möglich ... ohne dabei die kontrollierte Funktion des Ventilrückholsystems zu vergessen.
Abgesehen von der Kreisform der Ventile und Ventilsitze muss die Koaxialität der Ventilführungen, der Ventile, der Nockenwellen und der Nocken die Bewegung aller dieser Teile ermöglichen und gleichzeitig Folgendes ausschließen:
- parasitäre Reibungen
- das Gleiten der Ventilköpfe auf ihrem Sitz
- die Verstrebung der Nockenschaufeln in ihren jeweiligen Gehäusen.
Entgegen allgemein akzeptierter Vorstellungen ist es nicht möglich, die Konzentrizität zwischen einem Ventilsitz und einer Ventilführung zu kontrollieren, indem man einen konischen Piloten in eine Führung drückt und diesen Piloten als Stütze für eine Konzentrizitätslehre verwendet. Noch unwahrscheinlicher ist es, mit derselben Technik ein Werkzeug zu verwenden, um ein Nockenwellen-Bohrungsgehäuse konzentrisch zur Ventilführung zu bohren, was die wesentliche Voraussetzung für eine gute Leistung des Motors ist.
Die Kinematik des NEWEN FIXED-TURNING® umfasst eine hydraulische Zentrierung der Zentrierzapfen, die eine Zentrierung der Bearbeitungsspindel mit einem Fehler von nicht mehr als einigen Mikrometern (µ = 0,001 mm = 0,000039 Zoll) ermöglicht.
Der FIXED-TURNING®-Pilot schränkt die Ventilführung nicht ein und berücksichtigt die Bearbeitungsfehler der Ventilführungen. In gleicher Weise muss bei der Bearbeitung eines Nockenwellenbohrungsgehäuses die Führungsachse der Nockenwelle beachtet werden.
Die Bearbeitung mit FIXED-TURNING® garantiert, dass der Ventilsitz, die Ventilführung und das Nockenwellenbohrungsgehäuse die gleiche Achse haben und perfekt ausgerichtet sind. Außerdem können sich die Teile bei Höchstgeschwindigkeiten bewegen, ohne Reibungen und unerwünschten Bremsungen ausgesetzt zu sein, die den Betrieb des Motors bei hohen Drehzahlen unmöglich machen würden, was einen schnellen Verschleiß und ein offensichtliches Risiko mechanischer Störungen mit sich bringen würde.
Die Bearbeitung der Führungen, Ventilsitze und Nockenwellenbohrungsgehäuse mit FIXED-TURNING® garantiert in Verbindung mit den verwendeten Komponenten (Ventile aus Titanlegierung, Spezialfedern, Spezialventilsitze usw.) eine ultraschnelle Funktion des Motors, ohne dass die Gefahr von Luftdichtigkeitsdefekten, Reibungsstörungen und Ölfilmrissen besteht. Auch das Paniken der Ventile, die nicht in der Lage sind, erhöhten Betriebszuständen zu folgen, wird vermieden.
NEWEN FIXED-TURNING® ist ein Bearbeitungskonzept, das entwickelt wurde, um Bearbeitungsfehler auf Werte im Mikrometerbereich und nicht mehr im Hundertstelmillimeterbereich zu reduzieren.
Die Präzision der Koaxialitäten ermöglicht hohe Drehzahlen und eine optimale Funktion des Motors.
Der Koaxialitätsfehler der Achsen führt zu Bereichen mit erhöhter Reibung*, die die Bewegung verschiedener Teile verlangsamen, die Dichtheit der Zylinder zerstören und zum Festfressen führen, während die Drehzahl des Motors drastisch begrenzt wird. All dies wird durch eine Unwucht der Zylinder untereinander noch verstärkt. Jede Unwucht führt zu mechanischen Belastungen der beweglichen Teile, die zu vorzeitigem Verschleiß dieser Teile führen.
AUSPUFFPROFILE
Nach der Explosion des Gemischs (Kraftstoff-Brennstoff) füllen Restgase aus der Verbrennung den Zylinder und müssen durch die Auslasskanäle abgeführt werden, wobei sie vom Kolben ausgestoßen werden, der sich wieder seinem höchsten Punkt nähert. Das Auslassventil muss sich schrittweise schließen, bevor der Kolben wieder nach unten geht und dabei wieder etwas frisches Gemisch ansaugt. Diese Schließzeit ist für das Auslassventil kritisch. Auf eine extreme Temperatur erhitzte Gase werden zusätzlich zwischen dem Ventilsitz und dem sich schließenden Ventil laminiert.
Der Ventilsitz und das Ventil sind der Abrasivität der geschichteten Gase ausgesetzt und die Temperatur erreicht dann ihren Höhepunkt an den Oberflächen, die den Kontakt und die Luftdichtheit für einige Tausendstelsekunden gewährleisten. Damit dieser Kontakt nicht zu einer schnellen Abnutzung der Kontaktflächen führt, ist es notwendig, dass diese Kontaktbereiche eine optimale Oberfläche (mm2) aufweisen und ihre Formen komplementär sind (Winkel, Rundheit, Oberflächenbeschaffenheit usw.).
1. Stufenfreie Verbindungen mit einer Form, die den turbulenzfreien Fluss der Gase begünstigt.
2. Breite und auf das Ventil abgestimmte Sitzflächen für eine hohe Widerstandsfähigkeit gegen die abrasive Wirkung der Gase.
3. Venturi zur schnellen Ausdehnung und Beschleunigung der Gase.
NEWEN FIXED-TURNING® ermöglicht die Bearbeitung von Auslassventilsitzen, die groß genug sind, um sich nicht zu verformen, und gleichzeitig einen Winkel aufweisen, der dem des Ventils so nahe wie möglich kommt. Die runde Form ohne Facetten und Unebenheiten ermöglicht den Metall-Metall-Kontakt auf der gesamten Oberfläche des Sitzes, was einen guten Wärmeaustausch, eine perfekte Luftdichtheit und maximale Zuverlässigkeit gewährleistet.
Mit FIXED-TURNING® können Profile mit quasi unbegrenzter Länge bearbeitet werden. So können wir den Abgaskanal bearbeiten, um die Absaugung der Gase zu erleichtern, insbesondere die Venturirohre, die es den Gasen ermöglichen, direkt nach dem Passieren des Sitzes freigesetzt zu werden und so ihre Geschwindigkeit zu erhöhen. Scharfe Winkel, Stufen und Durchmesserunterschiede, die zu Turbulenzen und einer Verlangsamung des Gasstroms führen, werden beseitigt und jeder Kanal (Schale/Rückwand) wird optimiert und ist perfekt identisch mit den anderen Kanälen, um die Funktion des Motors besser steuern zu können.
EINLASSPROFILE
Im Gegensatz zu Auslassventilen und -sitzen sind Einlassventile und -sitze nicht der Laminierung von Verbrennungsgasen und dem daraus resultierenden Abrieb ausgesetzt. Einlassventilsitze müssen eine möglichst vollständige Füllung des Zylinders mit einem Frischluft-Benzin-Gemisch ermöglichen, das durch das Absenken des Kolbens angesaugt und möglicherweise durch die Wirkung eines Turboladers und eines Kompressors nach vorne gedrückt wird.
Die Form der Leitungen (Schalenbereich) muss optimal sein, um einen maximalen Gasdurchfluss zu ermöglichen, ohne dass parasitäre Turbulenzen entstehen. Der Winkel des Sitzes selbst trägt zur Führung des Gasgemischs bei und muss perfekt in die Gesamtform der Leitung integriert sein.
Abhängig von der Form der Kammern sollen die aus perfekt miteinander verbundenen Liniensegmenten und Radien bestehenden Profile einen optimalen Gasfluss ermöglichen. Scharfe Winkel werden vermieden und ein kohärentes Profil soll während der kurzen Öffnung des Ventils das größtmögliche Gasvolumen leiten. Die perfekte Abdichtung des Ventils soll eine optimale Verbrennung und Leistung sowie eine einwandfreie Zuverlässigkeit ermöglichen.
Only the FIXED-TURNING® allows the optimization of the intake conduit from the valve guide up to the edge of the cylinder. A machining with a perfectly mastered shape shall be carried out in one single operation and repeated identically for each cylinder. The original machining of the cylinder heads is carried out by a succession of complementary machining operations, valve seat housings, seat, machining of the angles… which automatically create irregularities harmful to the flow of gazes. The FIXED-TURNING® provides a continuous machining, without interruption, of the entire conduit, including the valve seat, which shall be machined without being subjected to the constraints of the remainder of the machining. The FIXED-TURNING® and the uninterrupted machining of the conduits and seats allows an optimum filling of the cylinders, a total regularity between the cylinders and, consequently, an optimum output of the engine.
1. Profile made up of line segments and radii optimizing the guiding of the mix towards the cylinder.
2. Seat perfectly round and air-tight with an angle prefectly adjusted to that of the valves.
3. Small anti-turbulance link radius.
4. Conduit shapes (Bowl) perfectly belnded and strictly identical between one another.
5. Raw material
6. Constant and smooth profile of the entire conduit (bowl), including the valve resting area of the valve.
REGULARITY OF THE FLUX AND BALANCING OF THE CYLINDERS
Each cylinder brings a proportional part to the power of the engine and only a perfect similarity between the power supplied by each cylinder shall allow an effi cient functioning of the engine at high RPMs.
Cylinders with perfectly identical behaviors shall allow to obtain an engine free of parasitic vibrations and shall allow elevated speeds.
NEWEN and the FIXED-TURNING® allow continuous machinings, regular and similar in all points, from one conduit to another, from one engine to another. The most sophisticated shapes are authorized in places where classic machining processes with form tools are powerless and ineffi cient.
NEWEN allows perfect valve seats and, consequently, an increased efficiency of each cylinder while permitting an exceptional reliability.
The respect of the machined depths is made possible by two particularities exclusive to the FIXED-TURNING®:
the FIXED-TURNING® allows machinings as small as
one hundredth of a millimeter (.00039”) on an entire profile, regardless of its length, while providing a perfect geometry of the seat (circularity, angle, concentricity…)
the numerical control of the FIXED-TURNING® autorizes depth adjustments within + or – 0.01mm (1/100mm) or .00039”.
The combination of these two exclusive possibilities allows to obtain perfectly identical combustion chambers that will give the engine its balance and its capacity to “rev at high rpms”.
These precision machining capacities exclusively guarantied by FIXED-TURNING® already permit the possibility to repair future engines integrating the HCCI technology (Homogeneous Charge Compression Ignition) that will revolutionize the gasoline engine by making it clean and very effi cient.
As a reminder, the HCCI technology allows to eliminate spark plugs, owing to the mastering of the compression of the air/gasoline mixture and, thus, by mastering an auto ignition of the combustible mixture. The consumption and power gains shall make this technique unavoidable. The machining of the cylinder heads will give a large part to the precision of the volumes of the chambers and machining depths. Only machining processes allowing minimal and extremely precise cuts shall be possible. The FIXED-TURNING® is already ready to meet this new challenge.
Performance and reliability go hand in hand
with precision and numerical control.
FIXED-TURNING®
ahead of its time?
No, the FIXED-TURNING® is right on time
to accompany engine specialists
desiring not to be outpaced by
technological evolutions.